Waterjet CNC Cutting
Abrasive Waterjet Cutting
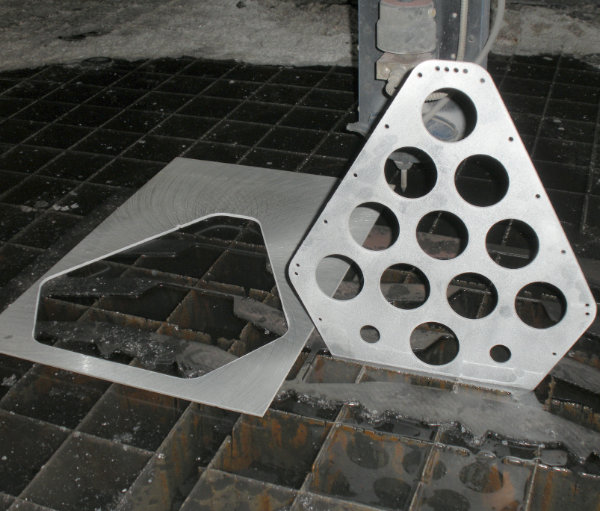
This is our method of cutting shapes from any type of material using high pressure water and abrasive. Water is pressurized to 50,000 PSI using hydraulic intensification, and then forced through a small orifice in the cutting head. At the head, abrasive is added to the water, creating a cutting stream which exits the nozzle at 1.5 times the speed of sound. Through a combination of micro-erosion grinding and shearing action of the pressure, a narrow cross section of material is removed all the way through the thickness. The process is then controlled via computer. Any two-dimensional shape from nearly any material is possible.
The resulting surface finish on the cut surfaces is far superior when compared to laser cut, torch cut or sawed surfaces. The process is non-evasive and does not work-harden the cut edges. Depending on material and dimensional tolerances desired, some sheet stock can be stacked for faster through-put.
WardJet 613
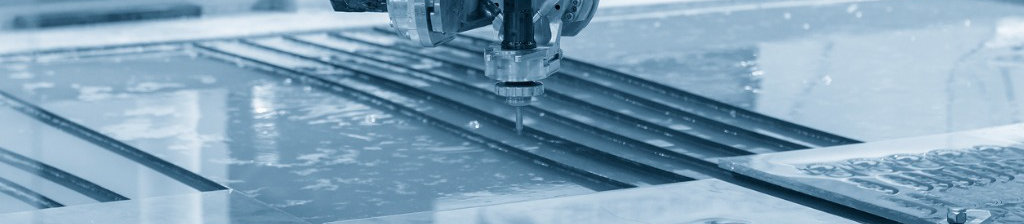
- Handles raw material sheet sizes up to 60 x 120 inches, and 5-inches in height.
- The process can cut virtually any material but is most cost effective when metal materials are under 1/2-inch thick.
- Accurately cut 2-dimensinal geometries within +/-.015.
- Equipped with two redundant 50,000 PSI high pressure pumps. Because this process is maintenance intensive, the two pumps allow us to keep production running while one pump is under repair—good to know if you are relying on predictable deliveries.
- Customer CAD drawings can easily be retrieved via email and sent directly to the machine over our network. This allows us to quote your projects quickly and ensures that your engineered drawings will be produced exactly as you have drawn them.
- Enables us to rapidly cut customer material requirements from our inventoried or procured raw materials and is usually the first step before moving on to our grinding departments.
- We are frequently asked to supply material, waterjet cut to near-net-shape and then grind specified surfaces, providing customers with one-stop-shopping for the "front end" of their projects.